NEWS
2022 / 12 / 02
Piston Ring Stock and Performance
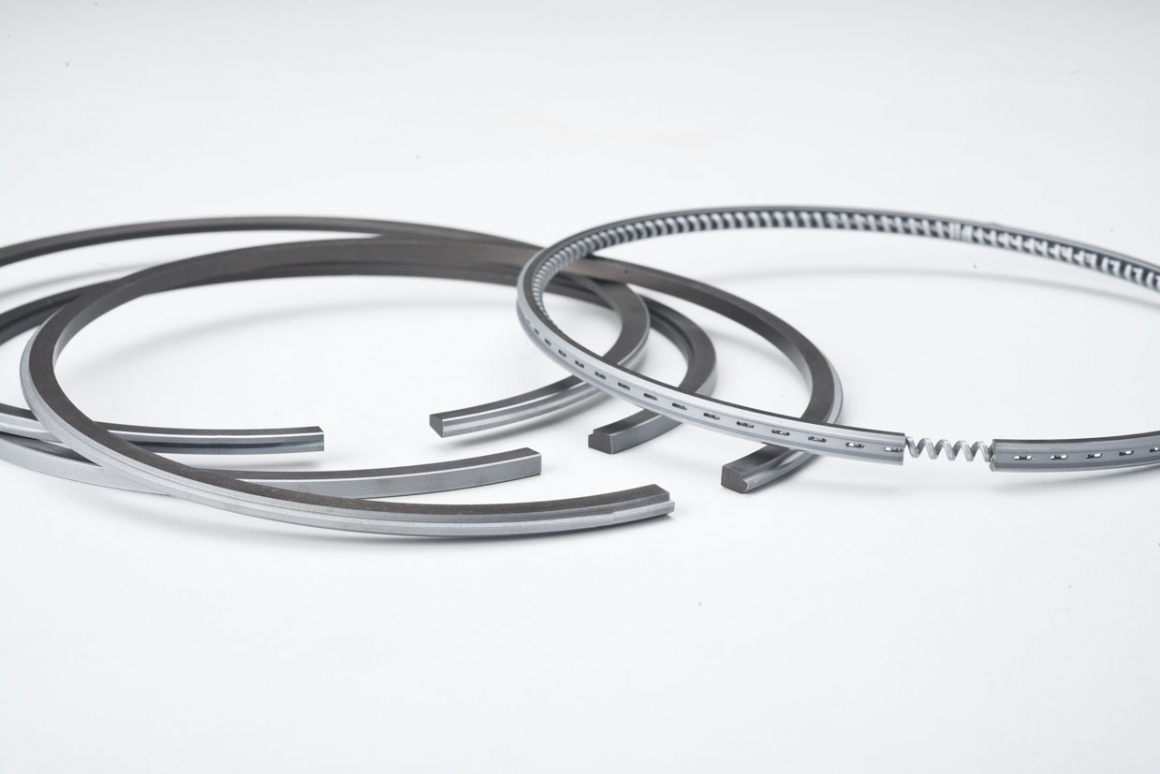
Piston rings have one of the toughest jobs inside an engine. They’re slammed up and down between the ring lands thousands of times a minute; they’re subjected to searing temperatures and extreme pressures; and they’re constantly scraping back and forth against the cylinder walls.
STOCK RINGS
With so many late model engines running thinner low-tension moly-faced ductile iron and steel rings, one might think cast iron rings are fading into history. They are at the OEM level, but it looks like cast iron rings will be around for a long, long time in the aftermarket. According to several ring suppliers, there is still a very strong demand for plain cast iron rings among engine rebuilders. The main reason is that cast iron rings cost less than more durable materials – and they hold up well enough in light-duty stock rebuilt engines.
The secret of using plain cast iron rings successfully is to thoroughly clean the cylinder bores after they have been finish honed. Plain cast iron rings don’t have a hard facing to resist wear, so they require a very clean surface. The cylinders should be washed and scrubbed out with hot soapy water to remove all traces of honing abrasive and metal residue from the surface. Using a plateau finish will allow the rings to seat almost immediately to extend life and reduce blowby.
LATE MODEL RING SETS
Ring sets in late model engines are running hotter than ever before. As rings move up higher and higher on the piston to reduce emissions, they are exposed to more heat. A decade ago, the land width between the top ring groove and piston crown was typically 7.5 to 8.0 mm. Today that distance has decreased to only 3.0 to 3.5 mm in some engines. This minimizes the crevice just above the ring that traps fuel vapor and prevents it from being completely burned when the air/fuel mixture is ignited (this lowers emissions). But the top ring’s location also means it is exposed to much higher operating temperatures.
The top ring on many engines today run at close to 600° F, while the second ring is seeing temperatures of 300° F or less. Ordinary cast iron compression rings that work great in a stock 350 Chevy V8 can’t take this kind of heat. That’s why many late model engines have steel or ductile iron top rings. Steel is more durable than plain cast iron or even ductile iron, and is required for high output, high load applications including turbocharged and supercharged engines as well as diesels and performance engines.
Under the top compression ring is the number two ring, which is the second compression ring. The number two ring assists the top ring in sealing combustion, and also helps the oil ring below it with oil control. Second compression rings in late model engines are still mostly cast iron because they don’t see as much heat as the top compression ring.
The third ring is the oil ring. This is typically a three-piece ring that helps spread oil on the cylinder wall for lubrication and scrapes off the excess oil to prevent oil burning. In three-piece oil rings, there are two narrow side rails and an expander that wraps around the piston. The expander exerts both a sideways and outward pressure on the side rails so they will seal tightly against the cylinder walls.
LOW TENSION RINGS
Over the years, rings have been getting smaller and thinner. Typical ring sizes today in domestic engines are 1.2 mm for the top compression ring, 1.5 mm for the second ring, and 3.0 mm for the oil ring. Some are even thinner. The Japanese are going even smaller. Some Japanese engines now have 1.0 mm and even 0.8 mm top compression rings.
Engine manufacturers have been going to smaller rings because the rings alone can account for up to 40 percent of an engine’s internal friction. Thinner rings exert less tension against the cylinders. This reduces friction and improves fuel economy.
Low tension rings also weigh less and reduce the reciprocating mass that pounds against the piston grooves with every stroke of the piston. But groove pound out and microwelding are still a concern because of the higher operating temperatures in today’s engines. To counteract this, some rings have a special coating on the sides to keep them from sticking as they bounce up and down in the piston groove. And the pistons themselves have been improved to make them more heat resistant and durable.
CHOOSING THE "RIGHT" RINGS
The right ring set can not only make more horsepower, but also improve the engine’s durability. Both are just as important on the street as on the racetrack. The best advice here is to follow your ring supplier’s recommendations. Use street rings on street engines, and performance ring sets on racing engines.
One of the newest trends in piston and piston ring selection is specifically matched components, delivered together in the same box. Leading manufacturers say this takes the guesswork out of selecting rings, makes for better weight-matched rotating assemblies and includes top-quality products for ease of assembly and maximum performance.
The type of ring materials and coatings that work best in a given application will depend on the engine’s compression ratio, the type of fuel it is burning (gasoline, alcohol or nitro), how much horsepower per cubic inch the engine will hopefully make, and the engine’s rpm potential.
For example, plain cast iron rings should never be used in an engine that burns alcohol because alcohol cuts lubricity. Coated rings are a must with alcohol.